Why is One Slot Longer Than the Other in My Electrical Outlet?
Q: Why is one slot longer than the other in my electrical outlet?
A: At first glance, this question makes me chuckle. “This’ll be easy,” I think. It strikes me as childlike, a “Why is the sky blue?” sort. You know the kind of question: simple on the surface, barely warranting a second glance. But when you try to dispatch it, it doesn’t budge. And dive a bit deeper, there’s an iceberg-sized topic, with massive safety implications, waiting below.
The short answer to the question is, we are talking about the polarized receptacle and its counterpart, the polarized plug, which has one wide blade and one narrower blade. The different blade widths ensure they’ll fit together only one way.
Of course, it’s a safety design. But why does it have to make life so difficult?
If you’ve ever struggled to plug something into a receptacle outlet only to find you’ve been holding the plug upside down, you are not alone. So maybe the better question is, why do we need the polarized plug and receptacle? Read on to learn more.
Uneven Slots are the Hallmark of a “Polarized” Receptacle
In General, receptacles and attachment plugs provide both a safe and convenient way to temporarily connect appliances into your electrical system. Removal is equally safe and convenient. Let’s discuss how the receptacle and plug connection has been a good idea from the beginning, and how the design has improved over the years to give us things like the polarized receptacle.
Consider an appliance such as a vacuum cleaner, designed for use with 110-Volts. It has a cord and plug for attachment to the electrical system, but the vacuum can’t be energized accidentally. It must first be plugged into a receptacle matching its plug. And, after using the vacuum cleaner, you can safely switch it off and disconnect it from the circuit by simply pulling the plug out of the receptacle. It can be stored in a closet with no fear of it causing an electrical fire. No power, no danger.
To add to the convenience, the appliance can be moved about from one location to another and plugged into an identical receptacle across the room. Off you go again, cleaning house. Meanwhile, back at all the receptacles, the live parts of the circuit are always safely recessed in non-conductive thermoplastic.
Sometimes, the things we take for granted can hurt us.
Imagine a housewife in 1946. She’s excited, because even though her house was built in 1926, she is the proud new owner of her very own electric vacuum sweeper. And she is the first on her block to have one.
One day she plugs in her vacuum and starts cleaning rugs. But the beater bar stops turning for some reason. Suspecting a broken belt, and being a mechanically inclined woman, she switches the machine off at the handle, kneels, and begins taking it apart to see what is wrong.
When she casually touches an exposed electrical connection, a sudden wrenching shock surprises her. It runs up her arm, down through her heart, and out her knee to the floor. Luckily, she manages to drop the sweeper and is not seriously injured.
But what happened? The machine was turned off, so how did it deliver that shock?
The answer turns out to be that her vacuum did not have a polarized attachment plug. In other words, one prong was not wider than the other. The plug could be inserted into a receptacle either right-side up, or upside down. In this case, it was plugged in upside down and the correct polarity was reversed.
When she turned off the machine at the switch and did not pull the plug, all the electrical parts of the machine stayed energized inside, except for the point beyond the switch where it was broken from continuing back into the receptacle’s neutral return slot. In other words, the return path was broken at the switch instead of the hot lead as it should have been!
The History of Polarity
Years ago, receptacle devices were made with two identical sized slots. In the United States, you can still find some pre-1930s vintage homes with these non-polarized, two-slotted receptacles. The symmetrical slots meant a lamp or other equipment could be plugged in haphazardly, with either prong becoming the hot path to the equipment.
Because household electrical current constantly changes direction, most equipment will run with the plug inserted either way. But as for safety, if the equipment has a manual built-in single pole switch or contains an Edison-style screw-shell for a light bulb, reversed polarity can create dangerous problems.
As with our cautionary housewife, any user, thinking that a switch in “off” position and an appliance not running means the appliance is safe, might be in for a shocking surprise. As a general rule, always cut the power before working on electrical wiring.
Over the years, there has been a steady progression of design improvements made for our electrical safety.
The polarized receptacle was one of the earliest improvements, created way back in the 1880s in Britain. One of its holes or slots was larger than the other, and this small improvement meant no more reversed polarity accidents. Sadly, the design was not put into wide-spread use in the United States until the 1930s.
It was even later, apparently in 1962, that the US National Electrical Code began requiring all receptacles to be both polarized and grounded. Finally, in 1969, Underwriters Laboratories mandated all new appliances manufactured with switches and/or screw shell light sockets had to be equipped with polarized plugs.
Today, the National Electrical code requires any cord and plug equipment to have either a polarized or three-pronged grounding-type plug, if it has any one or more of the following features: a manually operated single pole switch wired into the hot lead, an Edison-style screw shell for a lightbulb, or a built-in 15- or 20-amp receptacle.
Advances in electrical safety have led to further improvements in receptacles beyond the polarity design, but none have yet superseded its necessity.
Today, new design elements have been added to work together with the polarized receptacle and are already becoming widespread. One of these is the tamper-proof receptacle, which has a mechanism to prevent objects other than attachment plugs, such as screwdrivers or butter knives, from being inserted into one of its slots. This feature helps keep children safe in the home.
While all new homes are required to be fitted with tamper-proof receptacles, it is never too late to add them to your existing home. If you are updating, ask your electrician about installing them to replace your regular three-pronged grounded receptacles.
One more advance for safety that should be mentioned is ground fault circuit interruption. New electrical installations require protection by either GFCI receptacles or GFCI breakers in many areas in and around the home, but existing homes often need to be updated with this extremely useful device, as well.
One special benefit of GFCI technology: it is the only code-approved way for putting a three-pronged receptacle on an existing two-wire, non-grounded circuit.
NOTE: Any GFCI receptacle or GFCI-protected three-pronged receptacle without a connection to ground should be clearly marked with “No Equipment Ground” and “GFCI Protected.”
In Summary:
- Polarized receptacles and plugs are an important safety design for ensuring proper cord and plug connections.
- The main benefit of the polarized receptacle and matching plug is to ensure a hot to hot and neutral to neutral connection in equipment plugged into it.
- A non-polarized attachment plug may be a hazard. Your electrician can replace it with a safer polarized plug.
- Your electrician can replace your non-polarized wall receptacles with safer polarized versions.
- Both tamper-proofing and GFCI technology is available in polarized receptacle form. These advances further ensure your electrical safety when properly installed and functioning correctly.
- Test GFCI and all life-safety devices at least once a month.
Terminology
Receptacle – A connection device for allowing cord-and-plug equipment to be temporarily connected into the electrical system. Receptacles have slots and are the female part of the attachment pair.
Outlet – An accessible point in the electrical system where current can travel to-and-from to supply utilization equipment (such as a lamp, fan, or corded drill, etc.). Notice, an outlet is technically not the same thing as a receptacle, though the terms are often interchanged. Don’t worry. Your electrician should understand what you mean if you forget and say, “outlet,” when you really meant, “receptacle.”
Polarized – For our purposes, “polarized” means there are two differing sides designed to fit only one way in a connection. Using the term “Polarity” can be slightly confusing in describing electrical attachments, because there’s another use of the term. When speaking of household electricity, in the United States and some other countries, current “alternates” at 60Hz. This means the electrical polarity reverses direction 120 times per second.
* NOTE: If for some reason your receptacles were wired with “reversed polarity,” it really is a safety concern, and your electrician can detect and fix the issues. *
Plug – In the same way an ordinary plug is something inserted to stop a hole, the electrical “attachment plug” has prongs designed to fit into the slots of a receptacle. For this discussion, a “plug” is the male end of an electrical cord. You may have seen older equipment that did not have a polarized plug. Although it will still work in a polarized receptacle, your electrician can replace the plug end with a safer, polarized one. You may also choose to replace the entire cord with a new appliance cord.
Grounded – Connected to the earth or “ground.” Although the concept is simple, this term really deserves an article all its own. Modern house wiring now includes an extra wire attached at one end to a point in a distribution panel that is connected both to the earth and to the neutral path back to the utility transformer. The grounding wire travels along with the live circuit conductors to grounded receptacles. The grounded receptacle allows a three-pronged plug to be inserted. This is only one half of another safety feature in your electrical system, but as I said before, the subject deserves its own discussion.
GFCI – “Ground Fault Circuit Interrupter.” A GFCI is an electrical safety device that automatically interrupts, or “opens” a circuit when it detects current imbalance between the supply and return sides of a circuit. When a GFCI trips and opens a circuit, it indicates that at least some of the electricity that went out to a load did not returning on its designated path. Maybe it went through a person’s body instead. GFCI protection can be delivered by either a special breaker to protect an entire branch circuit, or by a GFCI receptacle. Household GFCI receptacles are polarized and can usually be identified by their distinctive test and reset buttons. You should test GFCI’s monthly to ensure they are functioning properly.
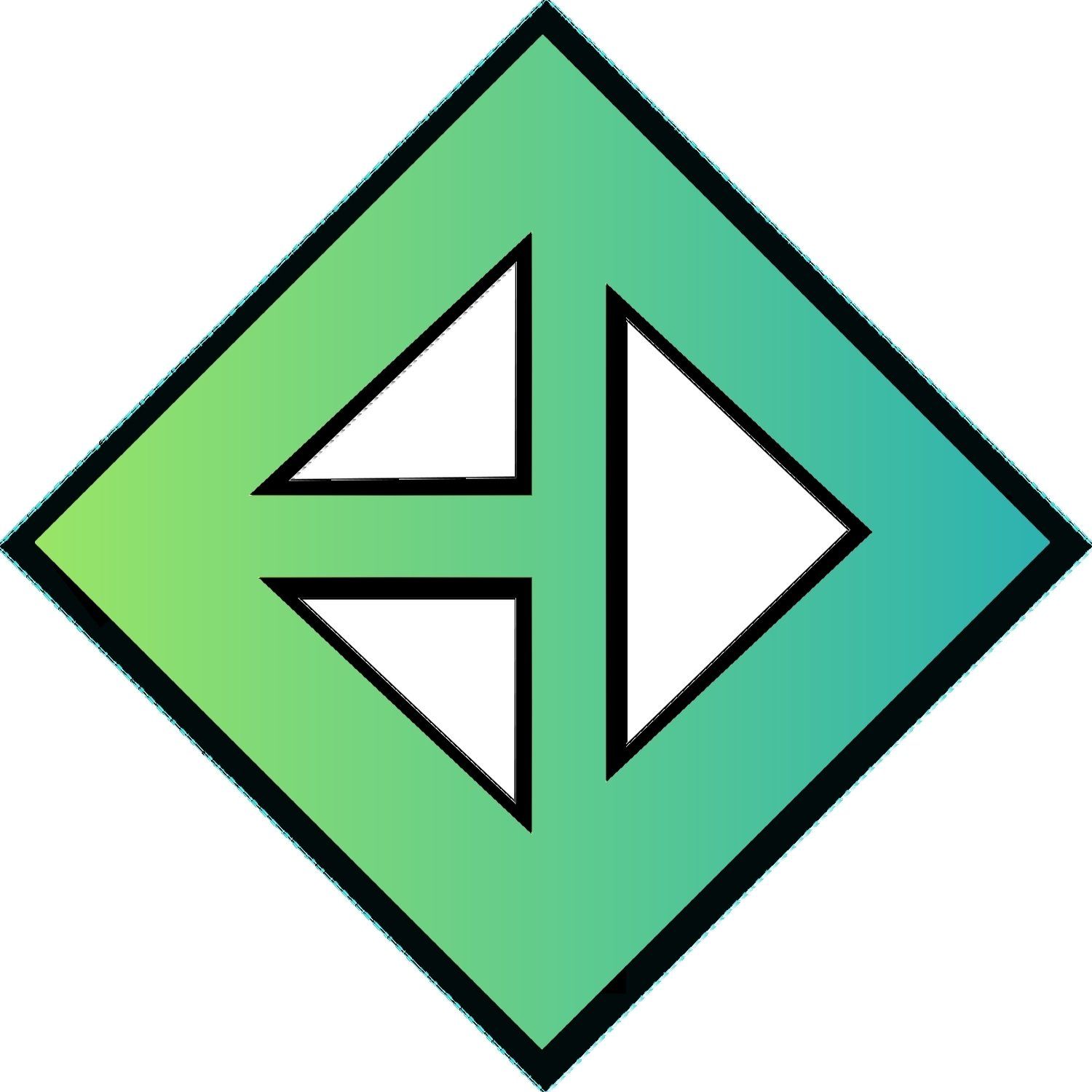
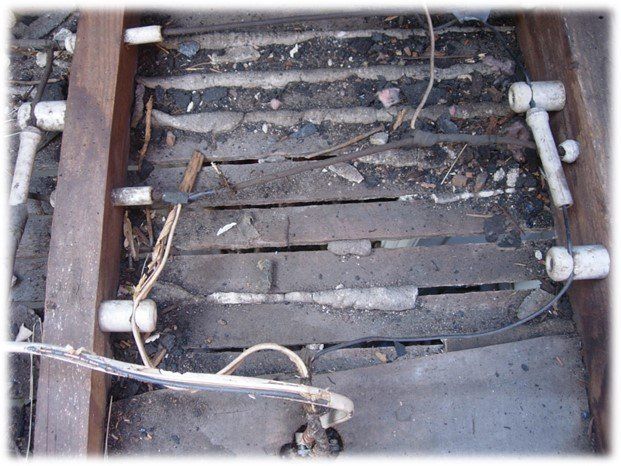